My research focuses on the processing and performance of composite materials. My research activities include:
Polymer matrix composite processing:
Process Modelling of Polymer Composites
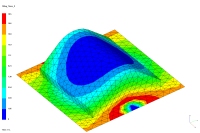
Resin pressure distribution during the resin transfer moulding of a carbon-epoxy bicycle part.
One of my main research objectives consists of developing comprehensive models of composites transformation processes that can capture the complex interactions between the different phenomena involved. These models will provide the foundation for understanding these processes as well as developing and optimizing new process variants. Processing models are developed from the governing equations for the physical and chemical phenomena involved during processing (i.e. heat transfer, cure kinetics, resin flow, fibre bed compaction and residual stresses). Computer simulations can isolate the dominant variables that affect the cure by means of parametric or sensitivity analysis. This approach can considerably reduce the number of plant trials required to achieve an adequate processing scheme for a complex part. As new material systems continue to emerge, this research will require extensive experimental materials characterization.
Investigation of Processing-Performance Relationship

Compression testing of a glass-vinyl-ester sandwich panel containing a process induced dry spot.
Processing research also addresses the problem of understanding and modelling the formation of defects and subsequently the effect of defects on mechanical properties. The ultimate goal of this research is to provide engineers and researchers with a set of modelling tools which will allow the design of composite parts considering manufacturing issues directly as part of the analysis. This becomes essential when designing tailored composite structures where curing residual stresses and processing defects can impact significantly the mechanical performance of the part.
Development of Polymer Composites Characterization Techniques
In order to apply process modelling, numerous material properties must be measured. The resin curing behaviour is correlated with other changes in other properties (e.g. viscosity, cure shrinkage, elastic modulus). Fibre preforms used in composite materials are also characterized to obtain the permeability and compaction as a function of fibre architecture and volume fraction.
Development of Polymer Nanocomposites:

Single-walled carbon nanotube ropes
To develop the next generation of aerospace structural materials, new advanced material forms must be investigated. The molecular structures of carbon nanotubes (CNT) and organo-clay platelets theoretically allow these materials to be utilized separately or in combination as the foundation of new material forms. Over the last decade, the research on carbon nanotubes synthesis, properties and applications have produced a massive amount of values for the properties of CNT polymer nanocomposites. The analysis of these results reveals a significant variability in the mechanical and physical properties mainly caused by the great difficulty of processing CNT with polymer matrices at CNT volume fraction greater than one percent. Issues with the poor control of the nanotube dispersion, alignment and interface with the polymer matrix are principally responsible for these disappointing results.
Therefore, this research consists to implement an integrated framework that includes modelling, processing and characterization to produce CNT polymer nanocomposites for macro scale and microelectromechanical systems (MEMS). This approach is essential for the development of new nanocomposite manufacturing techniques that will use the full potential of CNT as reinforcements. This effort requires the development of models that predict the physical, mechanical and processing properties of CNT polymer nanocomposites as a function of nanotube dispersion, concentration, purification, functionalization and orientation. Furthermore, the development of innovative manufacturing techniques to produce CNT nanocomposite structures is paramount. Finally, the characterization of processing, physical and mechanical properties is required to assess the quality of the produced nanocomposites.